Due to a more Lean waste management, Trivium reduces truck transport and delivers on its environmental credentials
Significant transport reduction due to waste handling changes
Trivium Packaging and Mil-tek worked together to create a waste handling solution that was more in line with the Lean principles currently being applied in the production, in order to stop sending waste to landfills.
An added benefit of this was that the internal truck transportation of waste was drastically reduced – by 60 %.
0%
Reducing landfill waste
Trivium Packaging is a global company that produces recyclable metal packaging for many different industries. Components for this packaging are delivered and packaged in paper, cardboard boxes, shrink wrap, and plastic banding before being assembled into the final product. This results in an enormous amount of generated waste.
Therefore, the company decided to – in one of their English factories – optimize their waste handling and also reduce the contribution of waste to landfill. So they brought in Mil-tek for help.
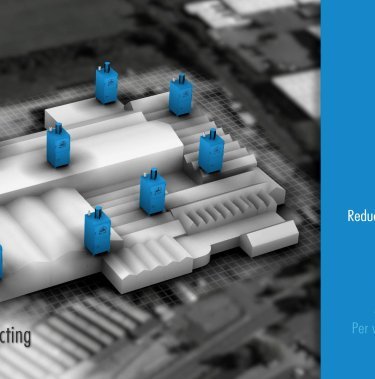
Waste problems on the factory
The current situation on the factory was that waste was collected around the facilities, and then transported by truck to outside containers several times during a day. The result of this was a lot of internal truck activity, creating risk of accidents, as well as mounds of waste being left out on the production line for collection, creating a messy work environment.
Furthermore, despite having a responsibility to keep the workspace tidy, workers frequently had to leave the production line to handle the constant flow of waste. Because of that, they were not carrying out their primary duties and overall productivity suffered as a result.
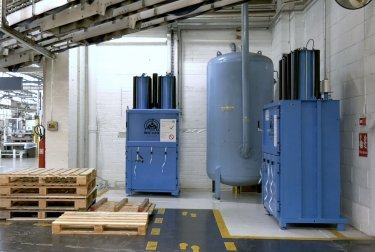
Mil-tek site survey and proposed solution
Recognizing the problems, Mil-tek started out performing an extensive value stream mapping on the factory. Obviously, a Lean manufacturing culture already existed, but it currently failed to reach beyond the production line.
According to the value stream mapping, each operator would walk 300 meters over forklift truck routes during a typical shift, over 10 times, to an external waste container. Eliminating this step was viewed as essential to resolving the overall problem, because it took time away from the production line that could have been used elsewhere.
By extending the existing ideology of 5S and compact the waste at source instead, Mil-tek demonstrated how much both travel time and mess could be reduced.
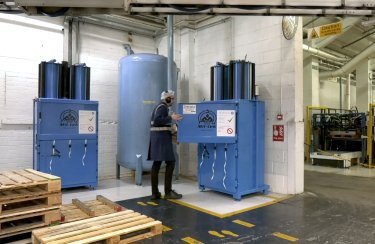
Installation of compaction equipment
Mil-tek installed pneumatic balers directly on the production line, on already existing air lines, in order to maximize efficiency. Now workers could dispose of waste directly on line, and did not have to move it by truck etc.
Since the machines reduce the waste by on average 10:1, the need for external truck trips to remove the waste was also drastically reduced.
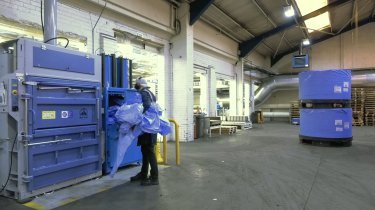
With the new waste solution, more benefits came
Since the first roll out, Mil-tek balers have been installed in six more locations around the factory. Today, the Mil-tek solution helps Trivium reduce its waste to landfill, and also to get nearer to achieving their goal of zero waste to landfill.
What began as a strategy to reduce waste, has resulted in much more than that:
- Financial savings
- Increased productivity
- A smaller environmental impact
- Fewer forklift truck movements, and therefore also lower risk of accidents
- Happier and more leaner workers
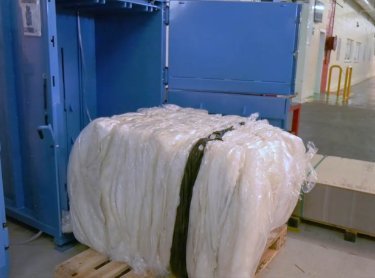
Can we help?
Get in contact with us to discover how Mil-tek can help your company handle waste more effectively and save a lot of resources.
Fill out the form and we will get back to you.